An Easy-To-Understand Guide to Types of Paint Sprayers
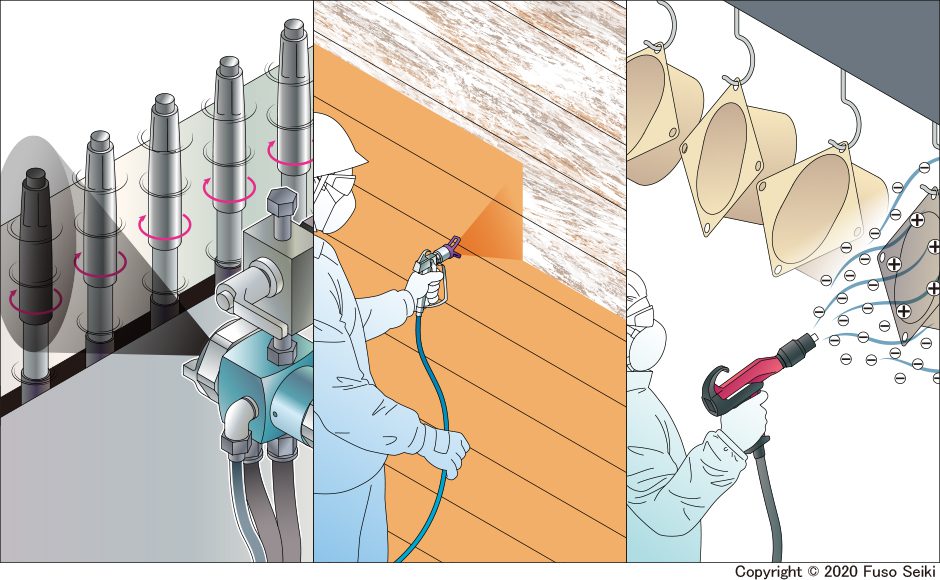
Spray guns are used for painting or coating. Although the different types of spray gun can be difficult to distinguish, they can be sorted into four varieties by painting method. Each type has its own advantages and disadvantages, and users will not be able to achieve the desired painting performance if the right type of spray gun is not selected. Here, we will explain the basics to be considered when one is thinking about using a spray gun. We will cover air, airless, electrostatic, and other spray gun types.
Do you know the differences between air spray guns, HVLPs and airless sprayers?
Speaking of spray guns, the first type that comes to mind are air spray guns (also called conventional spray guns) which finely atomize liquids by mixing them with compressed air. However, HVLPs, airless spray guns, and electrostatic spray guns can also be used for painting, and it is possible that most people cannot clearly tell the differences between them. Below, we will take a look at each type.
The classic spray gun for painting, the air (conventional) spray gun
Air spray guns
Advantages: Can handle wide variety of target objects and fluid types. Can create beautiful finishes.
Disadvantages: Overspray. Large amounts of Volatile Organic Compounds (VOCs) are emitted.
Transfer efficiency: 30% to 40%
Air spray guns were developed more than a century ago and still play a leading role for various painting applications, particularly in automobile manufacture. One factor that has made them useful for so long is their high degree of versatility. Compared to other types of spray guns, air spray guns can handle the greatest variety of target object shapes and fluid types. In addition, fluids that have been atomized by compressed air are uniform and create beautiful finishes. Air spray guns are still the first choice for painting applications because of their versatility, beautiful finishes, and affordability.
On the other hand, the main disadvantage of air spray guns is their low transfer efficiency. When atomizing with 0.2 to 0.3 MPa (30–40 psi) high-pressure air, transfer efficiency is only around 30% to 40% (see the note below). This means that they waste more than 60% of the coating used. Not only does this result in higher coating costs, the problem of high VOC (Volatile Organic Compounds) emissions from the use of solvent-based coatings is becoming more widely-recognized every year.
(Note) For painting, finely atomized fluid with high-pressure air reduces transfer efficiency. Even for air spray guns, transfer efficiency is significantly improved if low-pressure atomization of about 0.05 MPa (7 psi) is used. If you are considering air spray guns for other liquids such as lubricants, please refer to the link below : A Thorough Comparison of 3 Ways to Apply Lubricant When Stamping!
Overspray-preventing HVLP spray guns
High-volume, low-pressure (HVLP) spray guns
Advantages: Higher transfer efficiency than air spray guns.
Disadvantages: Not compatible with high-viscosity fluids. Slow for painting.
Transfer efficiency: 50% to 60%
High-volume, low-pressure (HVLP) spray guns were developed to avoid the problem of overspray encountered when using air spray guns. While air spray guns use high-pressure air to finely atomize fluids, HVLP spray guns spray fluids softly with air pressure reduced to around 0.05 to 0.1 MPa (7–14 psi). To compensate for lower air pressure and maintain atomizing performance, they use larger amounts of air instead. To supply air, there are types that use turbine motors and types that use air compressors.
HVLP spray guns excel at spraying varnish, enamel paintings, and metallic paintings, and they are often used to repair furniture, cars, and for do-it-yourself jobs. On the other hand, they are not compatible with high-viscosity fluids because of low atomization performance (for example, latex paints must be diluted before they can be sprayed). They are slower to paint with and are therefore unsuitable for professional applications.
Low-volume, low-pressure (LVLP) spray guns are overspray-preventing spray guns that use a concept similar to the one behind HVLP spray guns. They can be used with small compressors and are affordable, so they are suitable for beginners. However, they are only compatible with low-viscosity paints and have narrower coating patterns.
Airless spray guns are mainly used in construction, such as for exterior walls
Airless spray guns
Advantages: High painting speed. Can create thick coatings.
Disadvantages: They create rough finishes. Not suitable for painting small items. Ultra-high pressure creates injury risk.
Transfer efficiency: around 50%
Airless spray guns atomize fluids by applying hydraulic pressure instead of air. When using a garden hose, if you turn the water on all the way and partially cover the end of the hose with your finger, it increases the water pressure in the hose, causing the water to spray out. The airless spray gun atomization process uses the same principle. An ultra-high pressure of 10 to 20 MPa (1,500–3,000 psi) is applied to the fluid using a plunger pump or diaphragm pump. The fluid is then fed through a small hole at the tip of the nozzle, causing it to atomize.
The most prominent features of airless spray guns are that they can create thick coatings and have high painting speed. They are ideal for quickly painting target objects with wide surfaces such as exterior walls, fences, bridges, and ships. Overspray is relatively small and they are compatible with high-viscosity paints. These spray guns excel at outdoor painting applications for buildings.
However, with airless spray guns, drop sizes are large and finishes are rough. They also leave thick tails on both sides of the spray patterns, making them unsuitable for high-end projects. In addition, since their discharge amounts are large, they are unsuitable for painting small objects or coating small amounts of fluid.
There is also a type of airless spray gun called an air-assisted airless spray gun that features improved transfer efficiency. This is achieved by using a lower hydraulic pressure of about 3.5 MPa (500 psi). These spray guns use compressed air to eliminate uneven coatings caused by lower fluid pressure.
Electrostatic spray guns are high-tech spray guns with greatly improved transfer efficiency
Electrostatic spray guns
Advantages: High transfer efficiency. Paint envelopes target objects and adheres to back sides of target objects.
Disadvantages: Expensive. Depending on target object material and shape, it may be difficult to paint. There is a fire risk.
Transfer efficiency: 40% to 90%
Electrostatic spray guns offer the best transfer efficiency. A high-voltage current is applied to the tip of the gun, giving the fluid particles a negative charge. The fluid particles are then electrically attracted to the grounded target object, which holds a positive charge (when using the corona charging method). While it depends on the type of spray gun and other conditions, they can achieve a transfer efficiency of 80% to 90%. Electrostatic spray guns create beautiful finishes without air bubbles. They are used to apply primer surfacers, basecoats, and topcoats to automobile bodies.
Electrostatic spray guns offer excellent performance, but come at a high initial cost. One unit may cost 5,000 USD or more and requires a high-voltage generator, so the entire system needs a large investment.
There are also restrictions to the types of target bodies that can be coated. While coating fluid applied with an electrostatic spray gun can envelop the target object and adhere to its back, the Faraday cage effect makes it difficult for the coating to adhere to internal corners and recesses. Also, when coating non-conductive materials such as plastics, conductivity agents must be applied in advance.
Electrostatic powder guns have zero VOC emissions
Electrostatic powder coating guns
Advantages: Very high transfer efficiency. Can apply thick layers of coating. Environmentally-friendly with virtually no VOC emissions.
Disadvantages: Expensive. Cannot apply thin films of coating. Coating colors and varieties are limited. There is a fire risk.
Transfer efficiency: 70% to 95%
Above, we introduced air spray guns, HVLPs, LVLPs, airless spray guns, and air-assisted airless spray guns, but every variety also has electrostatic types. There are also electrostatic powder guns that are compatible with powder paints. The most popular among them is the electrostatic rotary bell atomizer. These atomizers are equipped with a bell cup that rotates at high speeds to atomize the coating agent with centrifugal force. After the powder paint adheres to the charged target object, the powder paint is melted in an oven during the curing process to form the coating film.
Powder paintings excel at creating thick coats. Therefore, they are mainly used for objects that must be durable and rust-proof such as fences, handrails, poles, and office furniture. Because this environmentally-friendly painting method does not use organic solvents, it is gaining popularity in Europe for applying clearcoats to automobile bodies.
Mapping seven different spray guns by performance
The spray gun types we have discussed so far can be charted by performance in two aspects, “Beauty of finish” and “Transfer efficiency.”
While electrostatic spray guns in the upper right of the chart may seem to be the best, one must keep in mind that they require high startup costs and are incompatible with certain types of materials. On the other hand, airless spray guns appear in the lower left quadrant, but their high speed makes them ideal for applications in construction. Please choose a spray gun that is best for your needs after considering the unique characteristics of each type.
(Note) Lumina (FUSO SEIKI Co., Ltd.) is a manufacturer of air spray guns.