Paint
Example 1
- User
- Major spring manufacturer
- Application
- Marking automobile springs
- Model used
- ST-6R-1.0X
Problem
This spring manufacturer produces springs for use in automobiles.
They had been using another company’s automatic spray gun to provide yellow lacquer as an identification marker.
However, that spray gun had a high atomizing air pressure which caused overspray of the coating, making it reach the opposite side of the target area.
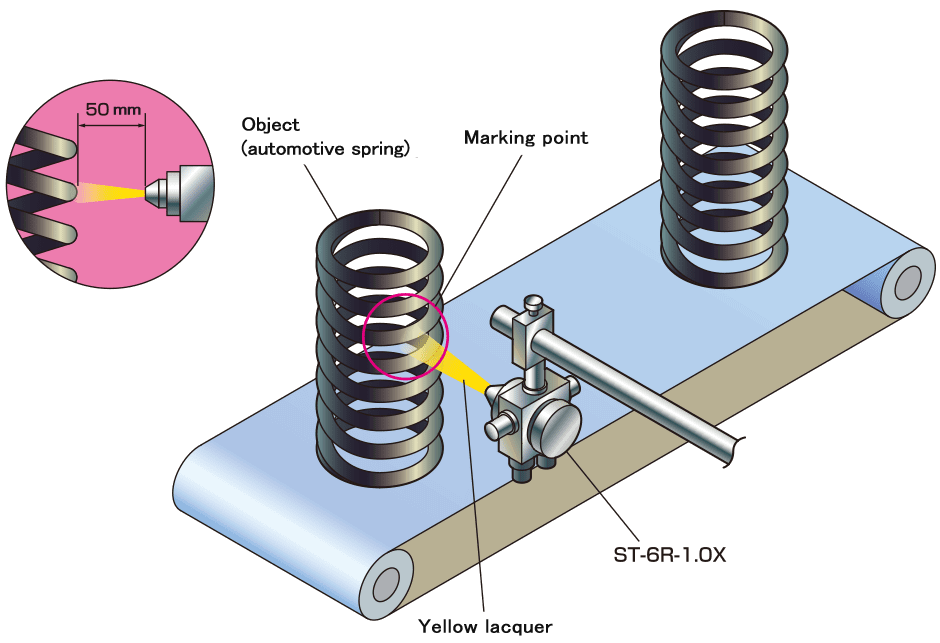
Lumina’s proposal and result
We proposed a standard round-pattern type ST-6R-1.0X spray gun. The original target distance was too long and, at over 0.2 MPa , the atomizing air pressure was too high. We decreased the target distance to 50 mm and lowered
the atomizing air pressure to 0.05 MPa.
- (Spraying conditions)
-
- Atomizing air pressure: 0.05 MPa
- Target distance: 50 mm
- Liquid supply: Pressure feed tank
As a result, the client was able to mark their products clearly without overspray.
Example 2
- User
- Container manufacturer
- Application
- Coating
- Model used
- ST-6-1.3X
Problem
This container manufacturer produces durable cylindrical containers made of thin cardboard layers for a client that produces powders. Since moisture could get in through gaps in the containers and ruin the powder, the client previously put the powder in vinyl bags before putting it into the containers.
However, this increased their workload, so the container manufacturer was searching for a way to coat their container interiors to prevent moisture from getting in.
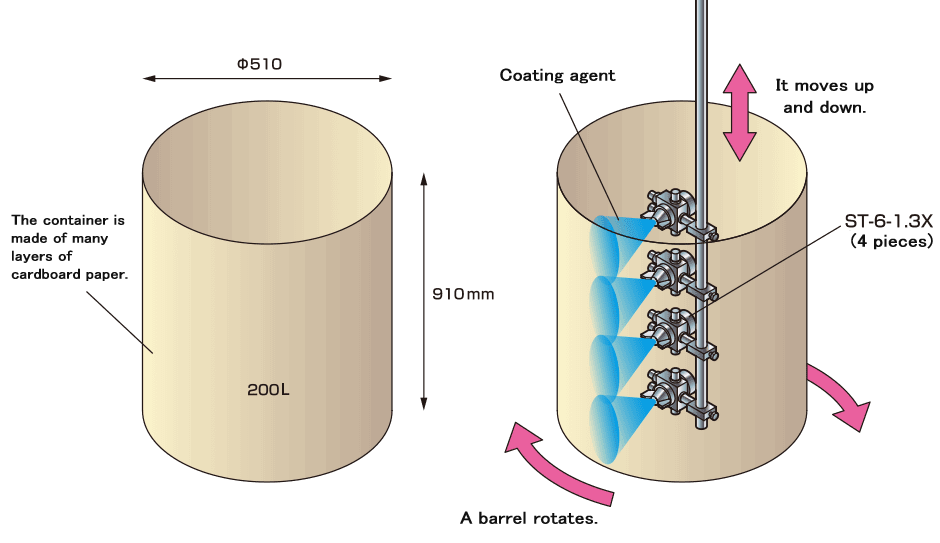
Lumina’s proposal and result
With an inside diameter of 510 mm , the containers provided plenty of space for spraying, so we recommended they install four ST-6-1.3X spray guns equipped with flat-fan pattern to rods to spray the coating liquid.
The system we proposed forms a layer of liquid on container interiors by rotating the containers while drawing the rod from their bottoms while spraying.
- (Spraying conditions)
-
- Atomizing air pressure: 0.15 MPa
- Liquid pressure: 0.3 MPa
- Target distance: 230 mm
As a result, the coating was able to prevent moisture from getting into the containers,
so the client was able to store their powder directly in the containers without using vinyl bags.
Not only did the container manufacturer win high praise from the client for cutting down on their workload, this became the first example in the paper container industry of a container that used an internal coating.
This made their product widely recognized as a high value-added product.