Release Agents
Example 1
- User
- Automobile parts manufacturer
- Application
- Aluminum die casting
- Model used
- HM-1、HM-3W
Problem
This manufacturer produces aluminum automobile wheels using die casting. Applying release agents makes it easier to remove completed products from molds, but the graphite in release agents frequently causes spray gun nozzles to clog. This can cause parts to become defective or production lines to stop. They asked for help to decrease the number of nozzle clogs.
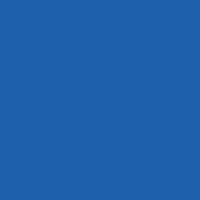
Lumina’s proposal and result
We proposed spray guns from the HM series based on the fact that its internal construction is suitable for avoiding graphite clogs in the fluid passageway. They installed two types depending on where they were needed on the production line: flat-fan pattern type HM-1 spray guns and spiral type HM-3W spray guns, which excel at coating the depressed parts of molds. As a result, the number of clogs and release agent shortages decreased, improving productivity.
Example 2
- User
- Electronics manufacturer
- Application
- Plastic injection molding
- Model used
- HM-1、HM-3W
Problem
This manufacturer uses plastic injection molding machines to produce mobile phone parts. Previously, they had used spray cans to manually coat the molds with release agent. Not only did this cause more work, the amount of release agent used varied from worker to worker, causing defects.
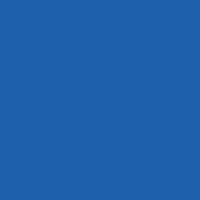
Lumina’s proposal and result
We proposed compact HM-3s which do not require much space to install. They were attached on top of the injection molding machines where they coated the molds at a
45-degree angle.
- (Spraying conditions)
-
- Atomizing air pressure: 0.25 MPa
- Target distance: 150 mm
- Liquid supply: 1 L gravity feed tank
Since the customer specified that the molds did not need to be recoated after every use,
we installed an AC-9 control box together with the spray gun to provide coating once for every five signals received. This saved labor and successfully decreased defects.