Why Too Much or Too Little Lubricant is Not Good for Press Processing
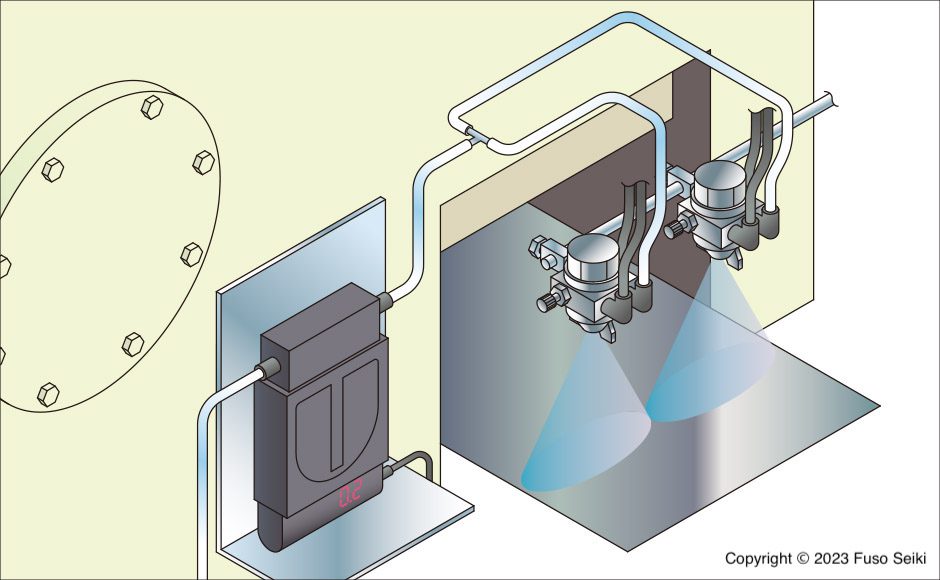
Applying lubricant to materials in press processing. Don't you think you should put on more? Insufficient lubricant is of course a problem, but too much lubricant also causes problems such as scrap jumping. These situations can lead to product defects and damage to the die. In this column, we explain how to apply an appropriate amount of lubricant to prevent such problems.
You Should Add More Lubricant, is Wrong
It is necessary to apply metalworking lubricant to the sheet metal during press processing. In press processing, a metal die is pressed against sheet metal using tens to hundreds of tons of pressure. Without metalworking lubricant, it is not hard to imagine that the product would be full of scratches.
Metalworking Lubricant Protects the Material with a Double Protective Film Layer
Metalworking lubricant prevents direct rubbing between the material and the die by forming an oil film on the surface of the material. In addition, components such as sulfur and phosphorus contained in the lubricant cause chemical reactions with the material, forming a chemical film that is resistant to abrasion and seizures. This double protective film layer protects the material from exposure to high pressure stress.
Not just sheet metal benefit from the use of lubricant. Friction with metal at high pressure also damages the die. As the die rubs against the sheet metal numerous times, it becomes hot and loses its strength, gradually becoming brittle and soon reaching the end of its useful life. When lubricant is applied to the sheet metal, the lubricant also sticks to the die, acting to reduce friction resistance while absorbing some of the heat, thereby reducing damage to the die and extending its life.
In this way, many workers are aware that lubricant is necessary for press processing. But did you know that too much lubricant should also not be used? Workers are sometimes worried they’ll run out of lubricant, so they think “let’s put more on.” In thinking this way, many workers set the liquid level of the lubricating roller to full. However, too much lubricant will increase lubricant costs and lengthen the degreasing time. Of these problems, what is most alarming is clogging of holes with waste and scrap jumping. In the worst case, this kind of trouble can damage the expensive dies, so paying close attention to prevent these problems is necessary.
Clogging of Holes with Waste and Scrap Jumping Caused by Excessive Lubricant Application
Clogging of holes with waste is a condition in which scrap generated by the punching process accumulates in the lower die. The die is originally designed to allow the punched scrap to fall downward, but for whatever reason sometimes the scrap is not expelled normally (illustration on left). The punch (upper die) repeatedly hits the area where scrap has accumulated, causing damage to the die.
Scrap that has accumulated in the drop hole leads to scrap jumping, which is an even bigger problem. Scrap that has accumulated inside the drop hole may stick to the punch and fall onto the sheet metal when pulled upward. In addition, scrap may stick to the back side of the moving sheet metal and infiltrate the gap between the lower die and the sheet metal. This is known as scrap jumping (illustration on right). When press processing is done while there is stuck scrap, the product can be dented, and in the worst case, the die damaged.
One of the causes of clogging of holes with waste and scrap jumping is excessive application of lubricant. If the thin plate scrap falls downward a little at a time, there will be no clogging of holes. However, the oily scrap clumps together in the drop hole and often becomes stick shaped. Clogging occurs because this scrap builds up in the narrow drop hole.
In the case of scrap jumping, this is also caused by the stickiness of the lubricant. No matter how much scrap accumulates in the hole, it will not jump onto the plate by itself. When the punch rises, the scrap that is sticky with lubricant is pulled up together, which is why scrap jumping happens.
For these reasons, the amount of metalworking lubricant applied should not be too much or too little. Thus, how can we be sure to apply an appropriate amount of lubricant? As introduced in the column “A Thorough Comparison of 3 Ways to Apply Lubricant When Stamping!” there are three main methods of applying lubricant. Of the three, the automatic spray gun is the most suitable for applying an appropriate amount of lubricant. The automatic spray gun uses compressed air to disperse the metalworking lubricant into droplets and spread them out in an oval shape. Since the spray gun is non-contact, it is possible to accurately apply an appropriate amount of lubricant. It can be said that this lubricant application method reduces the risk of product defects and die troubles and supports proper production management.
Using a Flow Meter to “Visualize” the Amount of Liquid
In industries that have strict production controls, such as the automobile industry, manufacturers of assembled products sometimes require precise numerical measurement of the amount of lubricant applied. In such cases, using a liquid flow meter in conjunction with an automatic spray gun makes it possible to “visualize” the discharge amount for each shot of spray (depending on the type and viscosity of the liquid, the use of a flow meter may not be possible).
It is often difficult to visually check the spray, so it is reassuring to be able to numerically confirm that the lubricant has been properly applied. Spray-gun operators often change the volume setting and spray more than is needed. If your goal is to apply an appropriate amount of lubricant, quantifying with a liquid flow meter is a useful method.
If you are searching for a method for applying metalworking lubricant, or if you would like to improve application accuracy, please feel free to contact Lumina.