A Thorough Comparison of 3 Ways to Apply Lubricant When Stamping!
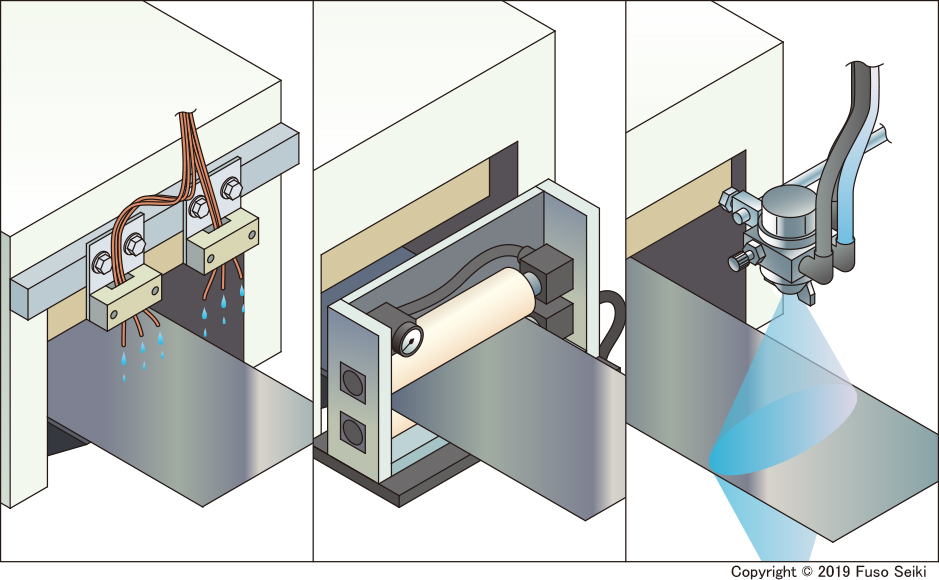
One essential step when shaping the work through metal stamping is lubrication of the material. The application of machining oil evenly and uniformly to the metal sheet prevents the scratches that can occur during stamping. However, there are in fact numerous lubrication methods. This article will introduce the characteristics of each of the three main methods, which are dripping, rolling, and auto spraying.
Why is lubricant applied to the sheet metal in the first place?
The metal stamping process supports numerous types of manufacturing, including that of automobiles, electronic devices, construction materials, and various fabrication machines. In the process, metal products are produced by forming the sheet metal, either blanking, bending, or drawing it by moving a punch vertically to apply strong pressure to the work.
When doing so, applying oil to the sheet metal is an essential step. As the punches and dies are pushed and rubbed strongly against the sheet metal, failure to use a lubricant will cause scratches from the friction. Furthermore, when working on stainless steel and titanium, the work can become burned or scored from the heat of that friction, and can even damage the die.
Reducing the friction between the sheet metal and die by forming a layer of oil film on the metal surface prevents scratches forming on the product while keeping damage to the die to the minimum. In other words, appropriate lubrication can reduce the defect rate while extending the life of the die.
Given this, what methods can be used to apply lubricant to the sheet metal? With the exception of manual brush application and spraying, there are three methods which are most commonly used. Those are dripping, rolling, and automatic spraying using a spray gun.
One simple method of supplying lubricant is dripping it from a copper pipe
Dripping is the easiest way to apply the oil. A copper pipe is attached to a glass oiler or oil tank and drips the oil onto the sheet metal by a gravity feed. The method can be installed cheaply and requires almost no maintenance, but this method’s greatest weakness is that oil can only be applied to a portion of the work.
Therefore, the oil is typically dripped from multiple pipes, or a felt roller is used to spread the oil to compensate. This method is also used on occasion in a supplementary fashion to apply oil to the portion of the work to which pressure is applied, such as with very thin sheet metal or material that is easy to process and would not normally need to be lubricated.
The roller, the standard lubricant supply method for stamping, has a weakness
The method used most often in the metal stamping process is the roller. In this method, a felt roller is saturated with oil and then brought into contact with the sheet metal to apply the oil to it. Unlike the dripping method, this method can be used to apply oil to a wider area of the sheet metal surface. The width of the roller is normally made to match that of the sheet metal in a range from 100 to 500 mm, but there are also large-scale devices with a width of 2 meters as well.
The problem with rollers is that the oil is applied unevenly. The application of oil becomes particularly inadequate in some spots when the felt roller becomes worn out. Workers on the floor are worried that defects will result from inadequate oil, so they will open the valve more to apply more oil. As a result, too much oil will be used. Fibers also fall from deteriorating rollers, and that can be another cause of product defects.
Furthermore, many users believe that while rollers can be used to apply oil to the reverse of the sheet metal, the amount applied is typically inadequate. The oil saturated into the roller can easily gather at the bottom of the roller due to gravity, leaving less oil at the top which comes into contact with the reverse of the sheet metal, which is disadvantageous.
Automatic spray guns can apply lubricant evenly
So what is the ideal way to supply lubricant when stamping? That would be the application of the right amount of lubricant to the right place. If there is not enough oil where it is needed, defects will result. However, if there is too much oil, costs will rise because more oil is used. Thus, the crux of supplying oil for stamping is the right amount in the right place.
Automatic spray guns are used in painting and coating, but they are also commonly used in the metal fabrication process as they can be used in a wide range of applications for applying liquids. Compressed air is mixed with each droplet of oil to break it up into smaller droplets which are then spread out to a specific width for application.
Thus, an automatic spray gun can apply a fixed amount of oil evenly to the work surface. The interval is controlled to apply oil just where it is needed. Of course, the oil can be sprayed up as well as down, so it is possible to apply an adequate amount of oil to the reverse of the sheet metal as well, so there is no need to worry about applying not enough or too much oil.
Does the spray gun cause overspray?
So what is the weakness of the automatic spray gun? One issue often pointed out is overspray. If the liquid is atomized too finely, it can fly off to the side before reaching the work, or bounce back if it strikes the work too hard. This causes overspray which can contaminate the surrounding environment and the workers.
However, this issue is not a concern because the quality of the spray can be controlled. The air pressure used to atomize the oil can be set as low as possible for a greater granularity of droplets resulting in a softer spray. Rain-like droplets will just reach and adhere to the sheet metal surface without contaminating the surroundings.
Use the right method for moisturizing your sheet metal!
There are three common methods for applying lubricant to sheet metal for metal stamping. Each has its own strengths and weaknesses, so it is important to choose the method that meets your requirements. Find the best oil application method to achieve smooth metal fabrication.