What to Do if Your Spray Gun Clogs
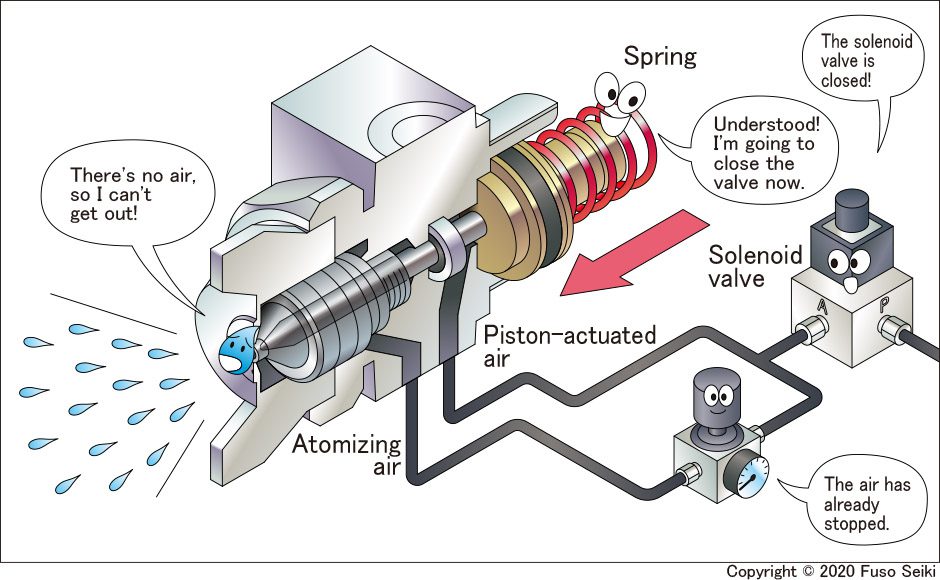
Clogging can become a problem when spraying paints and adhesives. If lines have to stop every time a spray gun keeps clogging, it can even hinder production. This column introduces seven tips to help solve issues with clogging (although the article assumes you are using fixed automatic spray guns, these concepts also apply to handheld spray guns).
Why do Spray Guns Keep Clogging?
So, why do spray guns clog? As you know, spray guns mix pressurized air with a liquid to create a mist. Liquid and air are sent to the gun separately and mixed at the tip to atomize the liquid. When liquids solidify, they can block the liquid or air passages, stopping the gun from spraying effectively. This phenomenon is also known as a clog.
Most clogs occur at the tip of the spray gun because the passage is at its narrowest in this area. Atomizing air sprays out from a gap between the air cap and the liquid nozzle. This gap is just a few tenths of a millimeter to 1 millimeter in width. If hardened paint or adhesive blocks this gap, it can prevent the liquid from atomizing correctly.
The liquid outlet is the first point where paint or adhesive comes into contact with the air and begins hardening. This combination of narrow passages and hardening liquid is why the vast majority of clogs occur at the tip.
Three Types of Clogs
Let’s examine this issue in more detail. Broadly speaking, there are three different ways that liquid can adhere to the air cap and harden.
The first is caused by liquid beginning to harden the moment that spraying starts. Paint or adhesive that has hardened will not spray out despite the force of the pressurized air. Instead, it ends up adhering to the air cap. This can be caused by the air pressure being too weak, which can stop the liquid from atomizing, or due to the liquid being of a type that quickly hardens once in contact with the air.
The second form of clogging is due to spray pressure being too high. A high spray pressure can cause liquid to bounce back and adhere to the air cap. This thin accumulation of paint particles on the cap causes the atomizing air passage to gradually become blocked.
Liquid can also adhere to the air cap after spraying stops. This issue can be difficult to detect. If you turn the spray gun on and off repeatedly while watching the air cap, you can see that the liquid outlet becomes slightly wet. This is due to the structure of spray guns.
In fixed automatic spray guns, compressed air has two uses: opening and closing the built-in valve (turning liquid on/off) and atomization. When the solenoid valve closes, the atomizing air turns off immediately. However, the spring takes a few tenths of a second to close the valve for the liquid (for more information on the structure of spray guns, see ‘Basic Structure’ and ‘Connecting the Spray Gun’ in the Operations Guide). This delay means that for a brief instant, the liquid is still coming out despite the supply of atomizing air stopping immediately. This can cause non-atomized droplets of liquid to adhere to the tip of the nozzle.
It’s easier than you think: Seven tips to help prevent clogging!
Here we will introduce seven tips to help prevent clogs from occurring.
Wipe the air cap
Use a different type of spray gun
Introduce time delays when atomizing
Soak the air cap in cleaning liquid when spraying stops
Adjust spraying distance and angle
Revise liquid paths
Prevent foreign matter from entering liquids
Wipe the air cap
This is a simple but effective method: Dampen a rag with paint thinner or liquid cleaning solution, then wipe the air cap and liquid nozzle outlet by hand. This type of cleaning may not be possible on an automatic line during operations. But even doing this when the line is stopped, such as during lunch breaks, is beneficial. This is because liquid most quickly hardens when spraying stops.
You could also attach a brush to the rod portions of air cylinders. The brush rubs against the air cap, creating an automatic cleaning effect (please ensure the brush is soft).
Use a different type of spray gun (different nozzle diameters, round, or spiral-shaped spraying)
An optimal choice of nozzle diameter and spray-gun type is sure to create improvements. The nozzle diameter refers to the diameter of the outlet at the tip of the liquid nozzle. The larger the diameter, the easier it is for the liquid to flow out, which can prevent clogs. You might also want to reconsider the spray pattern. Broadly speaking, there are two types of spray patterns, round or flat-fan (elliptical). Round patterns tend to clog less easily (the air caps on flat-fan types have more air holes, which increases the risk of clogging).
There are also round-type spray guns that create a spiral-shaped current when atomizing (the ST-6RW and MS-8B are two examples from Lumina’s lineup of automatic spray guns). These types use more power to draw up liquid, which can lead to fewer clogs.
Introduce time delays when atomizing
Time delays are another way to prevent clogging caused by the third type of clog, mentioned above. This method involves creating a slight delay when stopping the liquid on/off air (piston-actuated air, referred to as ‘CYL’ below) and the atomizing air. This requires a spray gun with at least two air inlets.
When the solenoid valve closes, the atomizing air stops slightly more quickly than the liquid, causing the liquid to remain at the tip of the nozzle. Separate solenoid valves can be attached to the CYL air and atomizing air paths to help prevent this issue. This will allow for the atomizing air to stop a few tenths of a second after the CYL air stops, which prevents liquid from being retained at the tip of the liquid nozzle.
Soak the air cap in cleaning liquid when spraying stops
When using paints and adhesives that quickly harden in the presence of air, it can be effective to soak the tip of the air cap in cleaning solution after spraying. This method prevents the liquid from hardening and dissolves already hardened material on the air cap, helping to prevent clogs. Before recommencing spraying, the gun should be sprayed momentarily to remove any cleaning solution adhered to the cap.
Adjust spraying distance and angle
Have you optimized distances and angles for the items in question? For instance, spraying a low-viscosity liquid at a distance of 50 mm with an atomizing air pressure of 0.2 MPa will cause the air cap to quickly become soiled due to bounce back.
Bounce back can be reduced by slightly increasing the distance, spraying at an angle, or reducing the atomizing air pressure to soften the spray.
Revise liquid paths
As well as the tip of the spray gun, another area that requires careful consideration is the liquid supply paths. If the liquid is high viscosity and the liquid paths are long, the liquid may clog up before it even gets to the spray gun. If this occurs, it may help to increase the diameter of the hose.
Supplying liquid to multiple spray guns means there will be branches in the liquid hoses. However, too many branches will cause the supply of liquid to become unstable. This can cause variations in the volume of liquid or may even stop liquid from reaching some of the spray guns. At most, only four spray guns should be supplied from a single tank. If you need to supply liquid to more guns, increasing the number of tanks will provide greater stability.
Prevent foreign matter from entering liquids
If foreign matter enters the liquid tank, it can cause the liquid passages to clog up and prevent the gun from spraying correctly. Foreign matter can enter the liquid when resupplying or can arise through liquid sediment building up at the bottom of the tank due to a long-time lack of cleaning. Periodic cleaning helps prevent the risk of clogs.
You may also need to select the optimal type of spray gun for the liquid being used, particularly if the liquid contains powder such as solid lubricants, mold-release agents with graphite, or metallic paints. A variety of improvements can be made, depending on your method of usage. Please contact us via our Contact page if you’re having issues with clogging.
Periodic cleaning of spray guns is crucial for ensuring stable operations. Maintenance manuals for Lumina’s automatic spray guns can be found on our catalog download page.