プレス加工の油塗布、3つの方法を徹底比較!
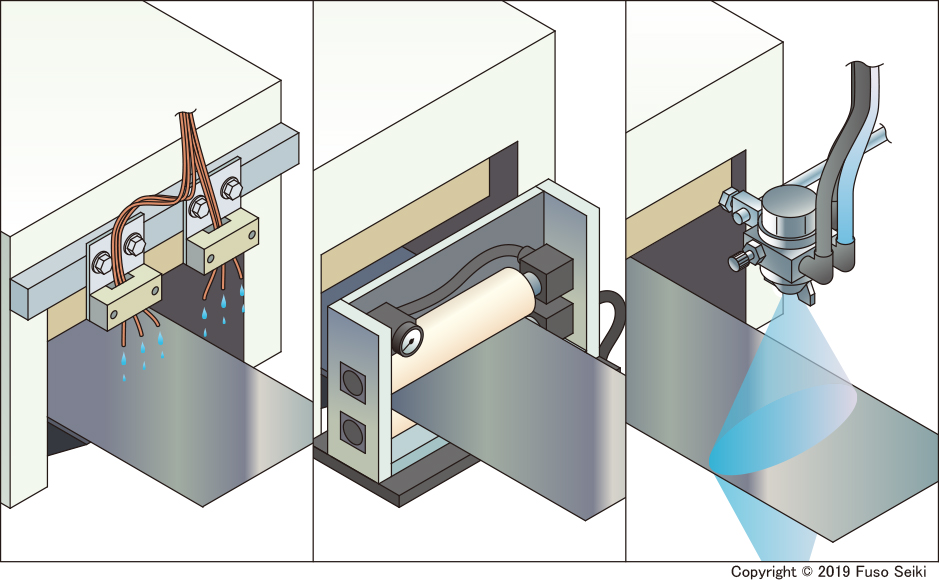
金属プレスの成型時に欠かすことができない板材への潤滑。加工油を板材に、ムラなく均一に塗布することで、プレス加工時に発生するキズを防止することができます。ただひと口に潤滑と言っても、その方法はさまざま。この記事では滴下(点滴)、給油ローラー、自動スプレーガンという3つの主要な方法(塗油機)とそれぞれの特徴をご紹介します。
そもそも、なぜ板材に油を塗布するのか?
自動車をはじめ、電子機器、建設材料、各種製造装置など、さまざまなものづくりを支えているのが、金属プレス加工です。上下に動くパンチが板材に強い圧力を加えることで抜き、曲げ、絞りなどの成型を行い、金属部品を生産します。
この際、板材に油を塗布することが不可欠となります。板材はパンチや金型に強く押し付けられ擦れ合うため、潤滑油なしには摩擦でキズついてしまうからです。また、ステンレス鋼やチタンを加工する場合、摩擦熱で焼き付きやかじりが発生し金型にダメージを与えることもあります。板材表面に油膜を形成し、板材と金型の摩擦を低減してあげることで、製品のキズを防ぐほか、金型のダメージも最小限に抑えます。つまり、適切な潤滑を行うことで不良率の低減と金型の寿命を延ばすことが可能になるのです。
では、板材への給油にはどのような方法があるでしょうか?手作業による刷毛塗りや霧吹きを除くと、最も普及している方法は3つあります。滴下(点滴)、給油ローラー、自動スプレーガンです。
銅パイプでの油滴下は簡易的な給油方法
滴下式は最も手軽な給油方法です。ガラスオイラーやオイルタンクを銅パイプにつなぎ、重力で板材に滴下させます。低コストで設置できメンテナンスもほとんどいりませんが、部分的にしか油を塗布できないことが最大の欠点です。そのため、複数のパイプから油を垂らしたり、フェルトローラーを併用して油を伸ばしたりすることが多いです。また、板材がかなり薄手で加工しやすい素材の場合に、負荷のかかる一部分にだけ塗布するといった、補助的な使い方も見られます。
プレス給油の定番、ローラーの死角
プレス加工の現場でよく使われているのが給油ローラーです。油を染み込ませたフェルト地のローラーを板材に接触させ、油を塗布します。滴下式と違い、油を板材表面に幅広に付けることができます。幅は板材の大きさに合わせた100〜500mm程度のものが一般的ですが、2メートル前後の大型の装置もあります。
給油ローラーで問題になるのが塗りムラです。特に、使用によりフェルトローラーがへたってくると、油の付きの悪い箇所が出てきます。現場の作業者は油不足で不良品が発生することを恐れるため、バルブを開いて油を多めに出すようになり、結果として多くの油を使います。劣化したローラーからは毛羽が落ち、製品不良の原因になることもあります。
また給油ローラーは板材の裏面にも油を付けられますが、裏面への油の付き具合が十分ではないと考えるユーザーは少なくありません。ローラーに染み込んだ油は重力によりローラー下部に集まりやすいため、板材裏面を塗るローラー上部には油が少なく、付きが悪くなるのです。
自動スプレーガンは均一に塗れる
理想のプレス給油とは、結局のところどんなものでしょうか?それは、適量の油を必要な箇所にだけ付けることです。油が足りなければ不良が発生します。逆に油が多すぎると使用量が増え、コストとなってのしかかります。必要な量を、必要なところに。これがプレス給油のポイントです。
自動スプレーガンは塗装やコーティングで使われる装置ですが、液体の塗布に幅広く応用できるため、金属加工の現場でも採用されています。コンプレッサーエアを混ぜることで1滴の油を細かい粒にばらし、一定の幅に広げて塗布します。
自動スプレーガンは、一定量の油を面全体に均一にスプレーすることができます。間欠制御により、必要な箇所にだけ塗布が可能。もちろん下から上へのスプレーもできるので、板材の裏面にも十分な量の油を付けることができます。油不足の心配も、油過多の恐れもありません。
スプレーガンは飛散する?
では、自動スプレーガンの欠点は何でしょうか?よく指摘されるのは飛散です。液体はあまりに細かく霧化されると、対象物に到達する前に脇から逸れていったり、対象物まで届いても勢いが強すぎてはね返ってしまったりします。これが飛散となって、作業者や周囲の環境を汚します。
しかし、スプレーの状態はコントロールできるので心配はいりません。霧化エア圧力をなるべく低く設定することで、粒子径の粗くソフトなスプレーを作ることができます。雨粒状の油がピタッと板材表面に付着し、周囲を汚しません。
最適な方法を選び、板材に潤いを!
プレス加工の板材給油でよく使われる3つの塗油機。それぞれに長所、短所がありますので、自分の求める条件に合致する方法を選ぶことが大切です。最適な給油方法を見つけ、「円滑な」金属加工を実現してください。